Exploring FDM 3D Printer Technology
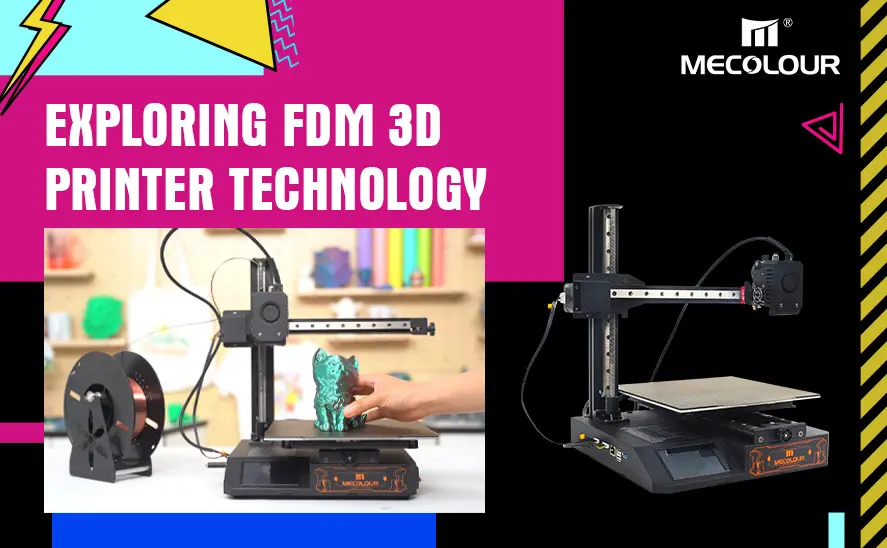
FDM (Fused Deposition Modeling) is one of the most popular and widely used 3D printing technologies today. Known for its accessibility and versatility, FDM is a favorite among beginners, hobbyists, and professionals alike. But what exactly is FDM 3D printing, and how does it work? In this article, we’ll delve into the FDM 3D printer technology, explore the materials and processes involved, and explain why this method is ideal for both newcomers and seasoned enthusiasts.
What is FDM 3D Printing?
Fused Deposition Modeling (FDM) is an additive manufacturing process that builds objects layer by layer by depositing thermoplastic material. It was first developed in the late 1980s and has since become one of the most accessible forms of 3D printing. FDM 3D printer technology is particularly popular because of its relatively low cost, ease of use, and the wide variety of materials available.
How FDM Works
FDM 3D printing involves feeding a thermoplastic filament into a heated nozzle, which melts the material. The printer then extrudes the molten plastic onto a build platform, where it cools and solidifies. The printer moves in the X, Y, and Z axes, creating each layer of the object according to the design file. Once one layer is completed, the build platform lowers, and the next layer is deposited on top. This process continues until the entire object is formed.
How To Use Mecolour FDM 3D Printer?
Materials Used in FDM 3D Printing
One of the key advantages of FDM 3D printer technology is the wide range of materials available. Each material has its own unique properties, making FDM suitable for various applications.
Common Filament Types
PLA (Polylactic Acid)
PLA is the most commonly used filament in FDM 3D printing, especially for beginners. It’s biodegradable, made from renewable resources like cornstarch, and easy to print with. PLA is ideal for creating prototypes, educational models, and decorative objects, though it’s not suitable for high-strength applications.
ABS (Acrylonitrile Butadiene Styrene)
ABS is a more durable and heat-resistant filament compared to PLA. It’s often used for functional parts and mechanical components. However, ABS requires a heated bed and emits fumes during printing, so proper ventilation is necessary.
PETG (Polyethylene Terephthalate Glycol)
PETG combines the ease of use of PLA with the strength and durability of ABS. It’s a popular choice for creating both functional and aesthetic parts. PETG is also resistant to water and chemicals, making it suitable for outdoor and industrial applications.
TPU (Thermoplastic Polyurethane)
TPU is a flexible filament that is used for producing rubber-like objects. It’s ideal for creating items like gaskets, phone cases, and flexible hinges. Printing with TPU requires careful calibration due to its elasticity.
Specialty Filaments
In addition to standard filaments, there are specialty materials designed for specific applications. These include:
Carbon Fiber Reinforced Filaments: For high-strength and lightweight parts.
Wood Filaments: For a wood-like finish on prints.
Metal Filaments: For metallic finishes and added weight.
Glow-in-the-Dark Filaments: For fun, novelty items that glow in low light.
The FDM Printing Process
Understanding the FDM printing process is essential for achieving successful prints. The process involves several key steps, each of which plays a crucial role in the final quality of the printed object.
3D Model Design
The first step in FDM printing is creating or obtaining a 3D model. This model is typically designed using CAD (Computer-Aided Design) software. There are also many online repositories where users can download pre-designed models.
Slicing
Once the 3D model is ready, it must be sliced into layers. Slicing software converts the 3D model into a series of thin layers and generates a G-code file that instructs the printer on how to create each layer. The slicing software allows users to adjust various settings, such as layer height, print speed, and infill density, to optimize the print.
Printing
With the G-code file prepared, the FDM printer begins the printing process. The filament is heated and extruded through the nozzle onto the build platform. The printer builds the object layer by layer, with each layer bonding to the one below it. Depending on the size and complexity of the object, this process can take anywhere from a few minutes to several hours.
Post-Processing
After printing is complete, some post-processing may be required. This can include removing support structures, sanding rough edges, or applying a finish to the print. Post-processing is particularly important for achieving a polished, professional appearance.
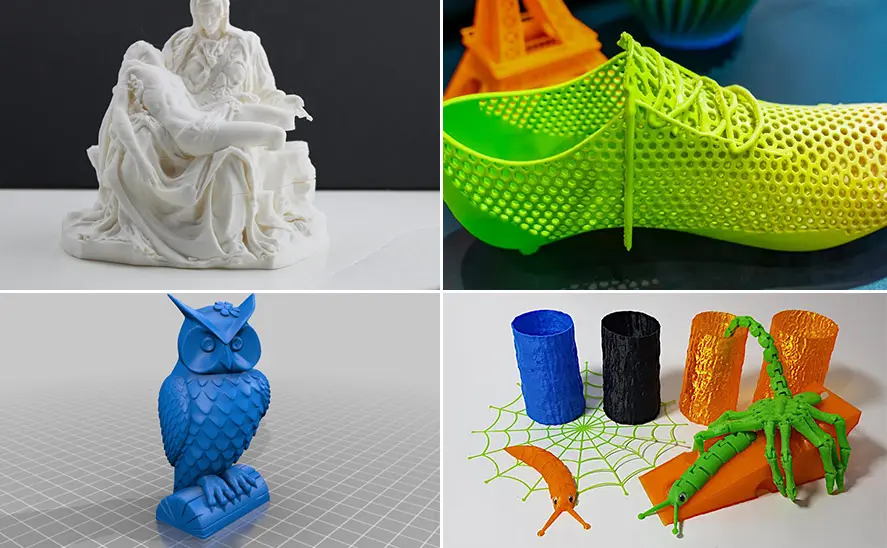
3d prints
The Future of FDM 3D Printing
As FDM 3D printer technology continues to evolve, we can expect to see further improvements in print quality, speed, and material options. The ongoing innovation in FDM printers and filaments will open up new possibilities for both beginners and professionals. Whether you’re just starting out or looking to expand your capabilities, FDM 3D printing offers a powerful and versatile tool for creating almost anything you can imagine.
Related:
Everything You Need to Know About FDM 3D Printers
The Magic Behind FDM 3D Printers: Unraveling the Mechanics